F-35 Report: Overview of Problems with F-135 Engine
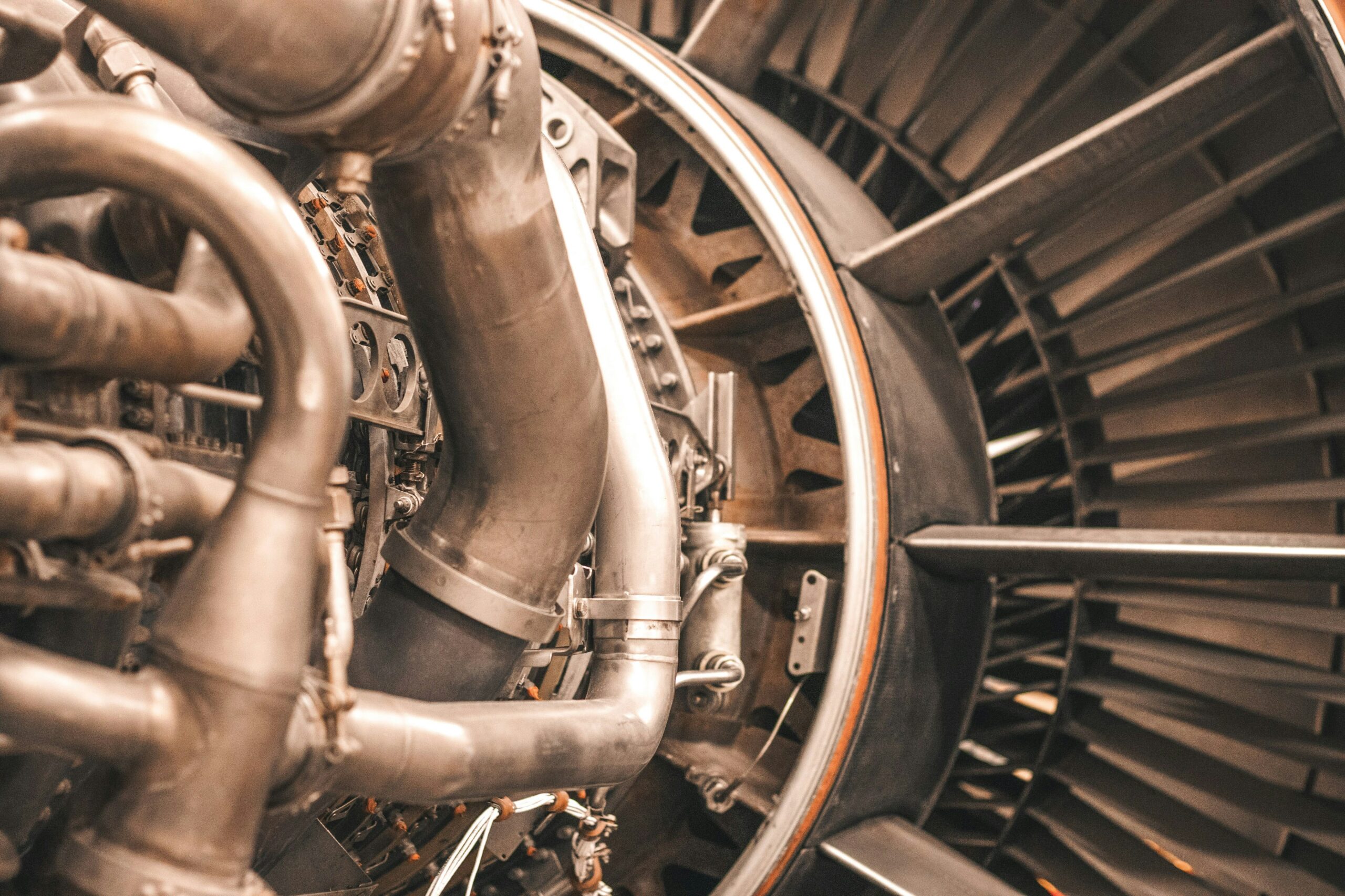
KESTEREN, Netherlands — Last week’s grounding of the F-35 fleet puts the Pratt & Whitney F-135 engine back in the public spotlights, just one week before the planned international debut of the F-35B at the RIAT 2014 and Farnborough Airshows. This renewed attention reflects long-standing concerns that the F-35’s engine can’t do the job.
Long-Running Engine Setbacks, 2007–2009
Between 2007 and 2009 the F-35 test schedule kept slipping. Breaks in turbine blades caused many groundings and forced Pratt & Whitney to change several engine parts that seemed solid on paper. A February 2013 fleet stand-down traced back to the same low-pressure third-stage turbine. Current investigators once more look at that blade row, suggesting the puzzle never vanished—only waited.
Analysts ask a direct question. Are these scattered breakdowns isolated, or do they reveal a deeper weakness in the F135 design? Operators also wonder whether every unit already delivered carries the same hidden risk.
Early Warning Signs Back to 2006
Evidence points farther back than 2007. Reports of engine stress surfaced the moment full-power runs began.
- May 2006: Aviation Week journalist David A. Fulghum wrote “Joint Strike Fighter F135 Engine Burns Hotter Than Desired.” He noted that higher gas temperatures might shorten engine life or trigger damage that standard inspections would miss.
- August 30 2007: Test engine FX634 failed after 122 hours. A blade in the third low-pressure stage snapped from metal fatigue.
- February 4 2008: Engine FTE06 broke a blade in the identical stage after only 19 hours.
Program officials labeled both failures “high-cycle fatigue testing.” Those words aimed to calm lawmakers, yet the setbacks slowed flight-test progress for more than a year.
2008 Instrumented Tests and Initial Redesign
In early 2008 engineers loaded ground-test engine FX640 with extra sensors. On April 21 they began a structured run plan, measuring forces across the power band. Data showed unusual vibration peaks during transitions on the F-35B “B-variant” when it shifted from wing-borne flight to vertical mode. Cracks formed at the same chord line every time.
Later that year the team pinpointed resonant vibrations as the trigger. Pratt & Whitney then:
- Adjusted the spacing between certain LPT blades.
- Strengthened specific root fillets.
- Updated the engine control schedule to alter spool-up timing.
After fresh trials the company re-certified the powerplant and announced the problem was fixed.
Fresh Trouble During 2009 Full-Power Runs
Confidence faded quickly. May 2009 runs uncovered pressure oscillations while the engine sat at low altitude, full afterburner. The team labeled the effect “screech” because a high-frequency tone accompanied the pressure surges. Until engineers installed fixes in 2010 the engine could not remain at maximum thrust for sustained periods.
In July 2009 Marine Corps Maj. Gen. David R. Heinz, then in charge of the Joint Strike Fighter Program Office, told reporters quality metrics still lagged. Too many blades missed dimensional targets, and entire blade “stacks” failed early life tests. Days later Pentagon leaders instructed him to stop public remarks on F135 quality.
September 11 2009 produced another headline. A newly built F135 broke down in a congressional budget season dominated by debate over whether to fund the rival F136 from GE and Rolls-Royce. Again faulty turbine hardware lay at the center. Pratt & Whitney blamed a bad bushing that nicked fan blades and promised a “minor modification” across all Initial Service Release engines.
Silence, Then Signs of Persistence in 2011
Program leaders kept talks about engine reliability private after 2009, and public updates grew sparse. Still, April 2011 brought a brief admission. Vice Adm. David Venlet confirmed some engines had slipped the delivery plan. Pratt & Whitney said a “small number” had swapped for spares since March because technicians found one mis-built ground engine and then traced the same assembly error to production units.
Twin Groundings in 2013
The F-35B fleet stopped flying on January 18 2013 when a fueldraulic line failed. Fueldraulics use jet fuel to move actuators that vector the nozzle, so a leak can start a fire. Investigators found a crimped tube. Flights restarted February 12.
A week later, on February 19, a routine borescope check of an Edwards AFB F135 revealed a crack in the third-stage low-pressure turbine. Lab work at Middletown, Connecticut, confirmed the finding. This led to a fleet-wide grounding when a cracked turbine blade grounded the F-35 fleet. The next day the Pentagon halted all F-35 sorties. Command released a short note on February 22: every airframe would stay parked until engineers understood the crack’s root cause.
Chronology of Major F-135 Incidents (2006–2013)
- May 2006 – Temperature limits flagged in Aviation Week.
- Aug 30 2007 – FX634 loses LPT blade at 122 hr.
- Feb 4 2008 – FTE06 repeats the failure at 19 hr.
- Apr 21 2008 – Sensor-laden FX640 starts vibration mapping.
- Late 2008 – Pratt & Whitney releases redesigned blade set.
- May 2009 – “Screech” shows up under full burner, low altitude.
- Jul 2009 – Gen. Heinz voices concern over blade stack rejects.
- Sep 11 2009 – F135 breaks during Capitol Hill debate.
- Apr 2011 – Program office swaps several mis-assembled engines.
- Jan 18 2013 – F-35B fleet grounded for crimped fueldraulic tube.
- Feb 19 2013 – Borescope at Edwards finds fresh LPT crack.
- Feb 21 2013 – Pentagon grounds entire fleet again.
Narrative Continues
During 2007–2009 test teams saw delays mount whenever a blade fractured. Engineers pulled engines, shipped them for teardown, installed replacements, and waited for data. Each pause forced software, avionics, and weapons trials to shuffle.
The February 2013 crack revived memories of 2007–2008. Same stage. Same region on the blade. Metal fatigue signatures looked familiar in lab photos. Although Pratt & Whitney built the cracked part after the 2008 redesign, investigators held conclusions until they finished strain-gauge checks.
Some observers frame the issue as a random cluster of industrial errors. Others see a pattern tied to intrinsic loading in that turbine stage. Even mild resonance, magnified across several flight profiles, can seed micro-cracks that propagate fast during high-cycle use.
Aviation Week’s 2006 warning about gas-path heat hinted at a broader margin-shortfall. When combustor exit temperatures rise a few dozen degrees, downstream parts face extra stress. That stress may not cause immediate breakage, yet it narrows safe life.
Throughout 2009 Pratt & Whitney tuned fuel-system pressurization logic to cure “screech.” They also patched control code to ease spool rates. The company stated the updates fixed the pressure pulse on test stands and in flight. After several sorties, pilots confirmed they could stay in full burner without unexpected throttle rollback.
The July 2009 quality-control dispute centered on manufacturing yield. Inspector records showed higher-than-planned reject rates for individual blades. Amid these ongoing setbacks, F-35 engine unit costs continue to grow despite efforts to streamline production. Engineers argued statistical spread would shrink once line workers settled into steady rhythm. Gen. Heinz pushed for better scrap numbers before declaring the problem closed.
When the Pentagon asked him to avoid public criticism, transparency advocates cried foul. They claimed silence shielded cost overruns, yet internal documents later released through auditing offices confirmed sustained attention on blade fatigue.
The September 2009 failure landed as Congress weighed the F136 alternate engine. Supporters of dual-source procurement seized on the timing, arguing competition would hedge technical risk. Opponents called the incident a distraction and kept the budget line trimmed. In 2011 the F136 program ended.
Replacement of several engines in early 2011 stemmed from an assembly mistake. Technicians reversed a fastening step during build-up of a ground test unit; auditors then discovered identical torque signatures on stock engines. Rather than re-work in situ, officials installed fresh modules to preserve the flight schedule.
The first 2013 grounding, linked to a fueldraulic tube, underscored how the F-35B’s lift-fan plumbing differs from that of the A and C models. Engineers stated the crimp resulted from mishandled tooling. Inspection of all 25 B-variant jets found no other crimped lines, though the fleet remained idle three weeks.
The second grounding spanned all variants. By then 51 aircraft sat across U.S. bases. Fleet managers feared a systemic flaw could force expensive retrofits. Metallurgists examined the cracked blade with electron microscopy, searching for tell-tale inclusions or machining marks.
By late spring 2013 interim clearance allowed limited flight in set regimes. Full clearance awaited stress-analysis updates in maintenance manuals and stricter borescope intervals.
Recurring Themes in the Data
Patterns appear when incidents line up on a timeline. Breaks happen at the same turbine stage, often early in service. Modifications improve life for a period, yet new loads arise when the aircraft envelope widens. Maintenance crews depend on revised inspection rules to stay ahead.
Blade geometry changed once in 2008 and again in 2010. Control software gained patches after both updates. Despite those steps, micro-crack discovery in 2013 proves margins remain slim.
Quality control also threads through the story. Mis-built lines, reversed fasteners, and defective bushings brought avoidable downtime. Each manufacturing lapse forced the program to replace parts that met drawing dimensions yet failed because of handling missteps.
Looking at Operator Impact
Flight-hour loss figures fluctuate by squadron, but every grounding cascades into simulator backlog, syllabus shifts, and contract penalty talks. Spare-engine pools run tight. When engines leave for depot work, training squadrons juggle tail numbers to keep pilot progression steady.
Some international partners keep extra propulsion modules in country to cushion delays, while others rely on U.S. depot turnround. Variance in logistics pipelines can translate into uneven flight hours among allies, even when airframes share block numbers.
Manufacturing Process Changes Over Time
Pratt & Whitney altered machining sequences after each blade incident. They introduced tighter non-destructive inspection at part-number gates:
- X-ray scan coverage increased on fir-tree roots.
- Automated eddy-current checks shifted earlier in the line.
- Final-balance specs widened traceability tags, pairing each blade to its disk.
Suppliers also upgraded alloy ingot batch records to tighten control over grain size and inclusion count. Yet the cracked blade from 2013 still passed all revised screens, implying that post-processing or in-service dynamics, not raw material, drove the flaw.
Maintenance Scheme Adjustments
After 2008 mechanics shortened hot-section borescope intervals. When “screech” surfaced in 2009 they added aft-frame thermal distress checks. The 2013 crack led to a fresh interval rule tied to throttle duty cycle, so aircraft that spend more time in burner receive earlier inspections.
The fueldraulic-tube crimp fix introduced a one-time visual in-tank check for B-variant jets, followed by random sampling during heavy maintenance windows.
Interchangeability Debate
Early in the program engineers touted high part commonality across A, B, and C variants. Once issues emerged, each fix sometimes applied to one model ahead of the others, eroding the value of common parts lists. That divergence increased logistics burden and complicated block-level retrofit planning.
Supply-Chain Ripple Effects
Blade scavenging during crack root-cause hunts pulled stock from production flow. New-build engines waited for missing parts, pushing delivery milestones rightward. Airframe assembly lines, paced to engine arrival, faced temporary idle periods.
Contract language includes clauses for such disruption. Penalty offsets appeared in quarterly selected-acquisition-report appendices, showing modest cost growth linked to propulsion delays.
Aviation Safety Board Involvement
Because turbine breaks threaten loss of thrust, the Navy and Air Force Safety Centers track each event. No F-35 crash yet ties to an F135 failure, but boards monitor trends to pre-empt mishaps. Findings feed directly into maintenance-order updates.
F-135 Setback in February 2013
The incident in February 2013 involved the tenth F-135 engine built. That powerplant had logged roughly 700 total hours, with 409 spent in flight on F-35A test airframe AF-2. Inspectors found a half-inch crack along one low-pressure-turbine blade. The location sat deep in the hot section, well past the fan, six compressor stages, the combustor, and the high-pressure turbine. Because debris must pass each upstream stage before touching the low-pressure blades, analysts ruled out classic foreign-object damage such as a bird strike.
On 6 March 2013 the Joint Strike Fighter Program Office briefed reporters. Spokespeople linked the fissure to thermal creep during supersonic runs at low altitude. Those sorties pushed the engine well beyond everyday line conditions, raised gas temperature, and kept the metal at peak stress longer than early models predicted.
Ground-Test Failure on 23 December 2013
Ground engine FX648 broke during accelerated-mission tests at Pratt & Whitney’s West Palm Beach site on 23 December 2013. The failure happened inside the first-stage fan integrally bladed rotor, often called a blisk. Engineers machine that disk and its blades from one titanium piece to trim weight and boost stiffness. In the F-135 the first ring uses hollow titanium, while the second and third rings rely on solid titanium.
Key facts about FX648:
- About 2 192 hours of total run time, the highest of any F-135 test unit.
- Roughly nine service years as a rig engine.
- Four-plus times more hours than the busiest operational F-35 engine in the fleet.
- Well ahead of the 622-hour benchmark held by the highest-time flight-test engine.
Lieutenant General Christopher Bogdan, the F-35 Program Executive Officer, told the House Armed Services Committee on 26 March 2014 that analysts had underestimated low-cycle fatigue stress. Later briefings repeated that point.
Pratt & Whitney issued a statement stressing ongoing review. The company said the event posed no direct risk to frontline squadrons and would not ground aircraft. By April 2014 technicians still lacked a confirmed root cause.
Oil-System Emergency and June 2014 Grounding
On 13 June 2014 a Marine Corps F-35B declared an in-flight emergency over Arizona. The pilot landed without injury at Marine Corps Air Station Yuma. Naval Air Systems Command later said a separated oil-inlet line at the oil-flow management valve caused a major leak. The fitting, labeled a Rosan connector, exists on every F-135 variant.
Authorities imposed a temporary fleet-wide stand-down. Checks on 104 airframes cleared most jets within days, yet inspectors flagged two additional engines as suspect and kept them idle for further work.
Severe F-35A Fire at Eglin, 23 June 2014
Ten days after the oil-line mishap, an F-35A from the 33rd Fighter Wing caught fire during takeoff at Eglin Air Force Base. Time of event: 9:15 p.m. local. The twin-ship training sortie aborted as soon as the instructor pilot sensed trouble. He shut the engine, exited unhurt, and the rescue crew smothered flames with foam.
Aircraft details:
- Tail AF-27, serial 10-5015.
- Low-Rate Initial Production 4 lot, first flight 22 April 2013.
- Delivered to the Air Force on 29 May 2013.
Investigators towed the jet into a hangar and collected runway debris for metallurgical review. No official photographs have emerged. Unverified field chatter suggested the airframe might be written off, though commanders have not confirmed that outcome.
One eyewitness, cited in local press, said fragments lay six feet around the jet and that “the engine tore through the top.” The account remains unofficial.
Eglin grounded its F-35As during the inquiry. Other sites kept flying until 3 July 2014, when the Pentagon declared the fire source lay inside the engine rather than the integrated power pack. At that point Department of the Air Force and Department of the Navy air-worthiness authorities ordered a full stand-down. They scheduled borescope checks for every powerplant and promised return-to-flight clearances after engineers parsed the data.
Investigators again circled the third-stage turbine wheel. That ring sits second within the low-pressure turbine and is common on all F-35A, F-35B, and F-35C engines. This same component was also involved when a catastrophic engine failure caused an F-35 fire.
Impact on Summer 2014 Commitments
Even as engineers scoped the damage, planners pressed ahead with display plans for Britain’s Royal International Air Tattoo at RAF Fairford and the Farnborough International Airshow. A go-or-no-go decision was penciled for 10 July 2014.
While technical teams hunted the fire trigger, acquisition staff froze contract talks for the next lot of engines. A Joint Program Office spokesperson told IHS Jane’s that negotiations for Low-Rate Initial Production 8 propulsion units would resume only after officials understood how the latest fault might ripple through price, spares, and support.
For context:
- The airframe LRIP 7 contract closed on 27 September 2013.
- The most recent engine award, dated 23 October 2013, covered LRIP 6 units.
- The LRIP 7 engine order had originally been slated for autumn 2013.
Chronology of Key Events, February 2013 – July 2014
- 19 February 2013 — Crack discovered in AF-2’s low-pressure turbine.
- 6 March 2013 — Program office blames thermal creep during extreme tests.
- 23 December 2013 — FX648 blisk fracture halts accelerated-mission runs.
- 26 March 2014 — Lt Gen Bogdan briefs Congress on low-cycle fatigue gap.
- 13 June 2014 — F-35B oil leak prompts fleet inspection.
- 23 June 2014 — F-35A engine fire at Eglin ends in emergency stop.
- 3 July 2014 — Pentagon grounds all variants pending engine checks.
- 10 July 2014 — Target date set for air-show participation decision.
Conclusion
Repeated failures in the same turbine stage point to more than chance. The pattern hints at a structural weakness inside the F-135 core. A future fleet-wide grounding would strip allied air forces of a large share of ready fighters, slow pilot training, and inflate support bills already stretched by tight defense budgets. Because F-35 squadrons will anchor NATO and U.S. air defense for decades, the engine’s health now sits on the desks of cabinet-level leaders.
Background: History of Previous F-35 Groundings
May 2007 — Electrical Short and Early Engine Worries
Prototype AA-1 lost power to its horizontal stabilizer after a 270-volt wiring short. Inspectors parked the jet and soon grounded the program. Engineers revamped sections of the high-voltage network and checked early F-135 builds for matching faults. Flight tests did not pick up again until December 2007.
July 2008 — Cooling Fan and High-Voltage Bus Faults
On 23 July 2008 both flying prototypes sat idle when ground crews found heat-exchanger fan wiring problems. By 18 August the Defense Contract Management Agency logged battery-charger, power-distribution, and controller glitches tied to the 28-volt and 270-volt buses. The fix package involved redesigned cards and safer routing. Flights restarted in the first week of September.
December 2008 — Engine Vibration and Seat Sequencer Issues
The fleet stood down on 12 December 2008 after test data showed non-spec vibration in the engine core and unexpected timing in ejection-seat firing. An escape-system trial on 20 November had revealed the sequencer mis-step. Engineers spent nearly three months validating new hardware and software. Prototype AA-1 returned to the air on 24 February 2009.
May 2009 — Suspected Engine “Screech” Instability
Starting 7 May 2009 all F-35 flying stopped. Witness reports linked the pause to “screech,” a pressure oscillation that emerges in the core at high power. Neither the Joint Program Office nor Lockheed Martin offered open comment. AA-1 flew again on 23 June 2009 after software damping and fuel-control tweaks.
October 2010 — Fuel-Pump Logic Error Above 10 000 ft
An F-35 climbed through 10 000 ft and the fuel boost pump unexpectedly shut down. Software logic risked starving the combustor and inducing a stall. Managers grounded the line while coders rewrote the sequence. Jets returned to normal schedules soon after the patch installed.
March 2011 — Dual Generator Failure and IPP Save
Test aircraft AF-4 lost both main generators on 9 March 2011. The Integrated Power Package kept flight-control computers alive, yet the fault triggered a fleet halt. Investigators blamed improper maintenance that damaged wiring. After checks the grounding lifted several weeks later.
June 2011 — Control-Surface Software Fault on F-35C
Naval Air Station Patuxent River paused carrier-variant flights on 17 June 2011. Lab runs had flagged a code path that might drive flaperons past limits. A revised load cleared the restriction by 23 June.
August 2011 — IPP Valve Failure Across 20 Airframes
On 3 August 2011 all 20 flight-worthy jets stopped flying when an F-35A’s Integrated Power Package valve jammed. Technicians allowed monitored sorties from 18 August while permanent hardware fixes went through the pipeline.
January 2012 — Repacked Parachutes in New Martin-Baker Seats
Fifteen jets fitted with -21 and -23 versions of the US16E seat stayed in hangars for about twelve days. Riggers found parachutes packed 180 degrees off design. Crews repacked the rigs and cleared each aircraft.
January 2013 — Fueldraulic Line Crimp in F-35B
On 18 January 2013 the STOVL variant went dark after a fueldraulic tube split. The line, crushed during manufacture, fed the nozzle-vector system. Repairs finished and the 25 affected aircraft resumed sorties on 12 February 2013.
February 2013 — Third-Stage Turbine Crack Across Fleet
A borescope on 21 February spotted a fracture in a low-pressure turbine blade at Edwards AFB. Commanders ordered every F-35 to park. Analysis traced the break to thermal creep under harsh test runs. Flights restarted once inspectors cleared each core.
June 2014 — Oil-Inlet Line Separation on F-35B
A Marine Corps pilot declared an emergency over Yuma on 13 June 2014 after a Rosan fitting on the oil-flow valve let go. The services froze flight ops, scanned 104 engines, and soon returned most jets to duty. Two powerplants stayed sidelined for deeper work.
June–July 2014 — Major Engine Fire in F-35A AF-27
On 23 June 2014 an instructor in AF-27 aborted takeoff at Eglin when flames burst from the tail. Ground crews doused the fire; the pilot walked away unhurt. Debris on the runway and witness accounts pointed toward a turbine break. Eglin grounded its wing, and on 4 July the Pentagon extended the stand-down to the entire program. Checks centered again on the third stage of the low-pressure turbine. Plans for British air-show appearances hinged on clearance expected 10 July.
Editor’s Note
Lockheed Martin and the Joint Program Office have never detailed another odd event from spring 2013. On 11 March that year F-35A AF-23 left Fort Worth bound for Nellis but diverted to Lubbock, Texas, when a cockpit warning lit. The jet then spent four weeks on the ramp while company technicians performed undisclosed work. It departed on 8 April. At the Paris Air Show three months later, Lockheed spokesman Michael J. Rein told Defense-Aerospace.com that a Program Office statement existed, yet no such release appears on record. The reason for the diversion, and the nature of the fix, remain unanswered questions.
THE F-35 ENGINE AND THE F-135 ECU DEVELOPMENTS – MARCH 2025 UPDATE
(original publication date remains July 09 2014)
Nine years have passed since the Eglin fire, and the fleet keeps growing. It now stands at 1,117 aircraft across 19 bases worldwide. Yet engine worries still dictate readiness rates. Three developments shape the picture.
First, the Pentagon locked in the F-135 Engine Core Upgrade. In October 2024 RTX’s Pratt & Whitney received $1.31 billion to mature new hot-section hardware, digital controls, and a more powerful power-and-thermal-management pack. The plan keeps the fan and outer casing but swaps bearings, combustor liners, and turbine airfoils for alloys rated above 3,600 degrees Fahrenheit. Flight qualification is due in 2029, with retrofit kits to follow.
Second, the cost picture worsened. A GAO review published in late 2023 showed sustainment estimates climbing to $1.58 trillion, up 44 percent since 2018. Engine depot throughput sits at 63 percent of required capacity because parts flow and skilled labor lag demand. Availability slipped again in 2024: the joint fleet averaged 51 percent mission-capable, far below the 70 percent goal.
Third, the adaptive-cycle alternative lost political momentum. GE’s XA100 met thrust and fuel targets, yet service chiefs rejected a dual-source path. The Air Force Chief of Staff told Congress that funding two engine lines would starve other priorities. Pratt’s upgrade now stands as the only funded solution, leaving GE to pivot the XA100 toward sixth-generation fighters.
Heat remains the headline issue. Block 4 sensors and jammers draw more electrical power than engineers foresaw a decade ago. A classified radar back-end due in Lot 20 needs an extra 14 kW of cooling on hot days. Aviation Week leaked internal charts that project a 62 kW thermal load by 2032, almost double the baseline. The Engine Core Upgrade promises 7 percent thrust and 30 percent more cooling, yet program insiders warn that gains will erode as soon as the next software block asks for more energy.
Field users feel the squeeze. Squadron logs show that power-module hot-section swaps now drive 43 percent of depot inductions. Consumable inventory cannot keep pace. A Marine F-35B squadron at Yuma rotated three jets to the back line last December because no F-135 modules were available after a surge in flight hours over the Red Sea.
Program leaders pin hopes on long-term contracts with fixed-price clauses that reward higher mean-time-between-removals. Lockheed and Pratt both lobby for performance-based logistics, under which contractors own spares pipelines and eat penalties when readiness slides. Congress has yet to grant blanket authority, but pilot unions back the plan, arguing that parts stability beats yearly budget roulette.
No new groundings have hit the whole fleet since 2021, yet local pauses still occur. Mis-torqued oil fittings halted five Norwegian jets for a week in February 2024. A fan-blade coating chip grounded a Dutch jet in May until a spare arrived from Oklahoma City. These cases rarely hit headlines yet drain training tempo.Bottom line: The F-135 still underwrites Western airpower, but margin remains thin. Several analyses now suggest that even the engine is compromised, raising concerns about long-term viability. The Engine Core Upgrade may buy time, not solve the core tension between heat and weight. Unless Block 5 shifts loads off the engine or brings radical cooling tech, maintainers will wrestle the same numbers in 2035 that they fight today.
REFERENCE SOURCES
- https://en.wikipedia.org/wiki/Pratt_%26_Whitney_F135
- https://www.flyingmag.com/aircraft-jets-turbine-blade-crack-grounds-f-35-fleet/
- https://www.ainonline.com/aviation-news/defense/2013-02-23/cracked-turbine-blade-grounds-f-35-fleet
- https://www.flightglobal.com/us-grounds-all-f-35s-over-engine-blade-crack/108865.article
- https://breakingdefense.com/2013/02/jsf-fleet-grounded-after-turbine-blade-cracks/
- https://www.wired.com/2013/02/engine-crack-stealth-fighter/
- https://www.airandspaceforces.com/f-35sgroundedafterenginebladecrackdiscovered/
- https://news.usni.org/2015/06/08/document-air-force-findings-from-eglin-f-35a-fire
- https://www.airforcetimes.com/news/your-air-force/2015/06/05/af-investigation-catastrophic-engine-failure-caused-f-35-fire/
- https://www.airandspaceforces.com/aib-report-on-f-35a-engine-fire-released/
- https://www.csmonitor.com/USA/Latest-News-Wires/2014/0704/F-35-jets-grounded-Fire-during-takeoff-grounds-entire-F-35-fleet
- https://www.f-16.net/downloads/F-35-AIB-Reports/10-5015.pdf
- https://www.bizjournals.com/washington/morning_call/2014/06/oil-leak-issue-grounds-f-35-joint-strike-fighter.html
- https://australianaviation.com.au/2014/06/f-35-fleet-grounded-for-oil-warning-checks/
- https://www.prattwhitney.com/en/products/military-engines/f135/engine-core-upgrade
- https://www.gao.gov/assets/gao-23-106047.pdf
- https://www.flightglobal.com/fixed-wing/overtaxed-f-35-engines-rack-up-38-billion-in-extra-maintenance-costs/153528.article
- https://www.dote.osd.mil/Portals/97/pub/reports/FY2014/dod/2014f35jsf.pdf
- https://www.dote.osd.mil/Portals/97/pub/reports/FY2015/dod/2015f35jsf.pdf
- https://www.everycrsreport.com/reports/R41131.html
- https://www.airandspaceforces.com/new-engine-core-upgrade-f-35-preliminary-design-review/