Underpowered Powerplant: The F-35’s Engine Can’t Do the Job
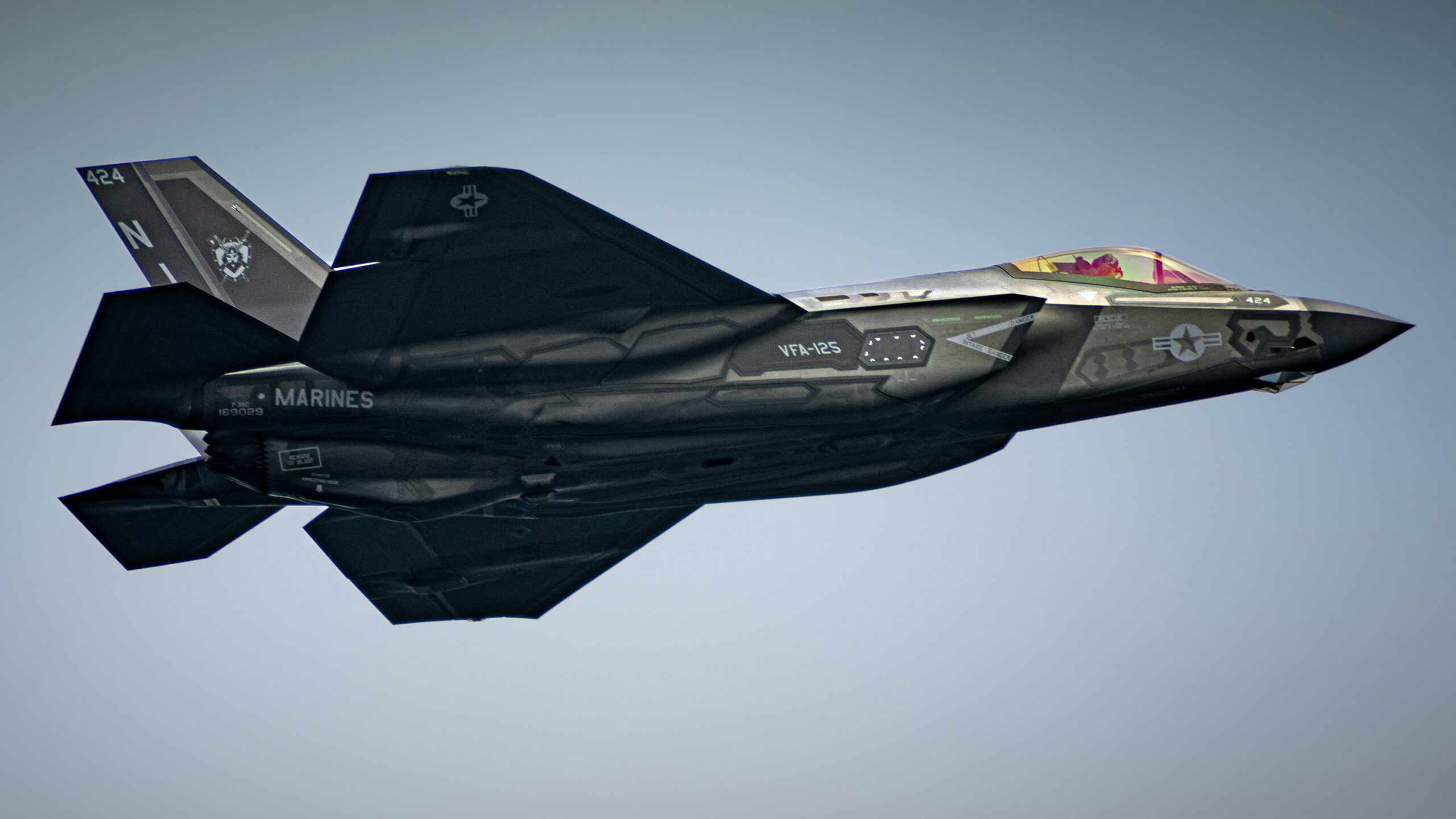
The single-engine F-35 keeps dragging the Pentagon into deeper trouble. Early budgets spoke about $233 billion for building the fleet. Today the ledger shows roughly $412 billion for 2 470 jets. Money keeps pouring, yet the fighter still can’t fly at full strength. A key reason sits right behind the cockpit: Pratt & Whitney’s F135 engine. Program leaders now admit the motor never met the real-world loads it faces, and every extra flight hour cuts its life shorter than planned.
F-35 Engine Design Flaws and Thermal Performance Shortfalls
Back in the design phase, planners set mild thermal limits. They guessed the aircraft computers, radar, and sensors would draw less power. Reality pushed harder. Avionics demanded more juice, so technicians had to push the core temperature past safe margins. That single choice started a chain of headaches. One consequence was the engine running too hot due to under-speccing, which exacerbated wear and forced repeated redesign efforts.
Common consequences show up fast:
- Hotter core gas flow wears turbine blades twice as quick.
- Higher cooling loads steal thrust that pilots need during climbs.
- Extra heat soak spreads stress into wiring and fuel lines near the tail.
Paper Trails and Slow Reactions
Lockheed engineers first saw the gap in 2008. They asked for a power boost by 2013. Managers pushed the idea aside, worried that redesign work would delay test schedules. A decade later, the jet still limps through development blocks, proving the delay cost more than time.
Selected Acquisition Reports even treat the engine as a stand-alone program. That odd split hides some dollars from direct view, yet analysts stitch the numbers back together. The tally shows maintenance costs climbing steeply. The engine earns its own footnote: it can fail five times more often than powerplants on legacy fighters like the F-16 or F/A-18. Nobody calls that acceptable, but no quick fix sits on the shelf.
F135 Jet Maintenance Backlog and Cold Performance Statistics
Fleet data from February tell a blunt story. Out of 564 delivered airframes, fewer than one-third could perform every assigned mission. The other jets sat grounded or carried limited status tags. Crews speak of swapping whole engines when they expected minor line repairs. Depot teams already face a queue that stretches months.
Because the F135 needs to run about 100 degrees hotter than the spec sheet says, parts like fourth-stage blades burn out early. One mechanic said the metal “looks tired long before schedule.”
The True F135 Engine Cost and Programmatic Impact
Taxpayers feel the pinch. Government Accountability Office staff peg the extra repair bill at roughly $38 billion across the fleet’s life. Break that down, and every U.S. citizen shells out a bit above $100 just to patch the engine’s premature wear. That figure does not buy new jets, new sensors, or even upgraded software. It only keeps current engines from failing outright.
Lieutenant General Michael Schmidt, who now runs the program office, calls cost “the biggest enemy we face.” He launched two parallel pushes: one aimed at flight readiness, the other at cost control. Critics reply that slogans fix nothing. Engines still flow back to overhaul bays sooner than planned, and crews keep cannibalizing grounded airframes for spare parts.
F135 Upgrade vs. Adaptive Engine Alternatives
Several years ago, General Electric finished a fresh adaptive-cycle engine that promised more thrust and better thermal headroom. Early bench tests looked solid. The new core could switch bypass flows to stay cool while meeting high power demand. Even so, the Pentagon canceled procurement in 2024, citing price pressure and schedule risk.
Supporters of the F135 insist the existing design can accept a “core upgrade” package. They talk about stronger materials and a denser fan stage. Skeptics doubt the plan. They point out that re-using the same inlet, nozzle, and mounts still ties the jet to narrow cooling limits. Without a larger heat sink, Block 4 software adds workload that drives the temperature problem right back up.
Thermal Management Wall
An F-35 must dump waste heat through fuel and intercoolers into the skin panels. Those paths already sit near capacity in warm climates. Once Block 4 adds new electronic warfare suites, analysts warn the thermal margin shrinks to zero. When the fuel no longer absorbs heat fast enough, avionics will command a throttle cut to protect components. That robs pilots of acceleration exactly when combat may demand it.
Engineers could add a bigger precooler behind the left weapons bay, but space is scarce, and weight creeps above limits. Meanwhile, Honeywell has targeted 2027 for delivering F-35 power and thermal upgrade systems to improve cooling headroom. Naval aviators see harsher stakes: on carrier decks, jets queue close together. If one plane runs a bake cycle at idle, heat plumes might damage nearby radomes. Flight-deck crews watch the exhaust line nervously during launch windows.
Fleet Impact by the Numbers
A quick look at key data points offers scale:
- Average engine removal interval: 1 600 hours (goal was 4 000).
- Depot induction backlog: 86 bare cores waiting strip-down in Oklahoma.
- Mean mission-capable rate: 29 percent (goal stands near 70 percent).
- Projected extra maintenance bill: 38 billion over 30 years.
- Current per-unit engine price: around $27 million, and that excludes spare modules.
International Knock-On Effects
Allied operators trust the U.S. supply chain. When depot slots dry up, overseas forces wait longer for refurbished engines, too. Norway temporarily stored two aircraft last winter, lacking serviceable powerplants. Australia flew ferry sorties under strict throttle caps to ease thermal stress. Small air forces cannot afford deep spares pools, so each delay hits training and alert rosters hard.
Foreign defense ministries grow wary. Initial agreements promised predictable sustainment costs. Pentagon contract reallocated ISR aircraft to Jordan after regional tensions rose, highlighting how external shifts can impact fleet logistics. Real bills now bite deeper into yearly appropriations, crowding out upgrades to bases and weapons stocks. Some partner nations quietly study life-extension options for older fourth-generation fighters, hedging against the F-35’s uncertain engine future.
Political Pressure Builds
Capitol Hill hears the complaints. Committees pushed the program office to outline a clear engine recovery timeline by late 2023. Deadlines slipped, and the F-35 program cost rose by $26 billion in the latest fiscal year, further fueling congressional concerns. Lawmakers talk about fenced funds in the 2026 defense bill if no credible remediation plan appears. That could freeze production slots, raising unit costs even more. The spiral feels familiar to veterans of past aircraft debacles, yet few officials want their fingerprints on a stop-work order.
Options on the Table
Planners sort through three broad paths:
- Status Quo Plus Patch. Keep the F135, integrate stronger blades, and insert thermal coatings. Cost sits lowest, but performance gains stay modest.
- Core Upgrade Package. Replace compressor and turbine modules, maybe enlarge the fan by small margin. Provides a bump in airflow and heat limit, yet still inside tight bay volume.
- New Adaptive Engine. Choose General Electric’s XA100 or a similar design, cut a fresh inlet duct, and accept long retrofit shutdowns. Up-front spending soars, yet the jet gains decades of growth margin.
Each path contains risk. The first risks permanent readiness drag. The third risks time. Decision makers lean toward the middle ground, but many engineers whisper that half fixes rarely solve full problems.
Training and Safety Ripples
High engine temperature raises safety stakes as well. Pilots who practice carrier landings under surge power profiles feel compressor stalls more often. Simulators replicate the margin, yet real-world flameouts still startle crews. A sudden power loss during vertical landing for the Marine Corps “B” model can wreck an aircraft in seconds. Investigators trace recent mishaps back to thermal fatigue cracks that escaped borescope checks, proving the maintenance model struggles to find hidden faults before parts fail.
Looking Ahead to Block 4
Block 4 aims to bring the jet close to its advertised combat punch: new radar modes, deeper electronic attack, and multicarriage of latest weapons. All that gear draws watts and adds heat. Without extra cooling, the software may throttle systems or shorten sortie duration.
Bottom Line for Warfighters
For now, squadrons craft work-arounds:
- Fly at night when ambient temps are lower.
- Use tanker support to avoid max-power climbs.
- Rotate tail numbers to spread engine hours evenly.
These measures keep training calendars alive, but they mask the core flaw rather than solve it. Warriors trust their kit to carry them home. Every unexpected engine swap erodes that trust bit by bit.
Pentagon projections already carve out billions for engine sustainment upgrades through 2035. That slice competes with next-generation drone projects and hypersonic weapons. At some point, leaders must choose whether to pour more cash into a legacy powerplant or bite the bullet on a fresh design. Observers fear drawn-out indecision could leave the fleet stuck in the middle, paying peak dollars while missing peak performance.
Final Assessment
The F-35 program still sells itself as the future backbone of allied air power. Engines sit at the center of that promise. Until the thermal choke point lifts, every flying hour feels like a gamble, every budget cycle feels tight, and every partner nation tracks the depot backlog with growing unease. Policymakers face a simple truth: powerplants that cannot meet spec drag the entire aircraft down, whatever fancy sensors ride in the nose.
If leadership wants a fighter ready for high-end conflict rather than PowerPoint slides, they must pick a clear engine path soon and stick to it. Delay only deepens the maintenance hole, and no slogan, war on cost or readiness, can patch a turbine that runs too hot for its own good.
REFERENCE SOURCES:
- https://en.wikipedia.org/wiki/Lockheed_Martin_F-35_Lightning_II
- https://www.twz.com/f-35-engine-running-too-hot-due-to-under-speccing-upgrade-now-vital
- https://www.reuters.com/business/aerospace-defense/rtx-unit-pratt-whitney-completes-preliminary-design-review-engine-upgrade-2024-07-15/
- https://www.flightglobal.com/fixed-wing/honeywell-targets-2027-for-delivering-f-35-power-and-thermal-upgrade/160069.article
- https://www.collinsaerospace.com/what-we-do/industries/military-and-defense/power-and-thermal-management/enhanced-power-and-cooling-system-epacs