Successful Flight Testing of ISRO’s Scramjet Engine Technology Demonstrator
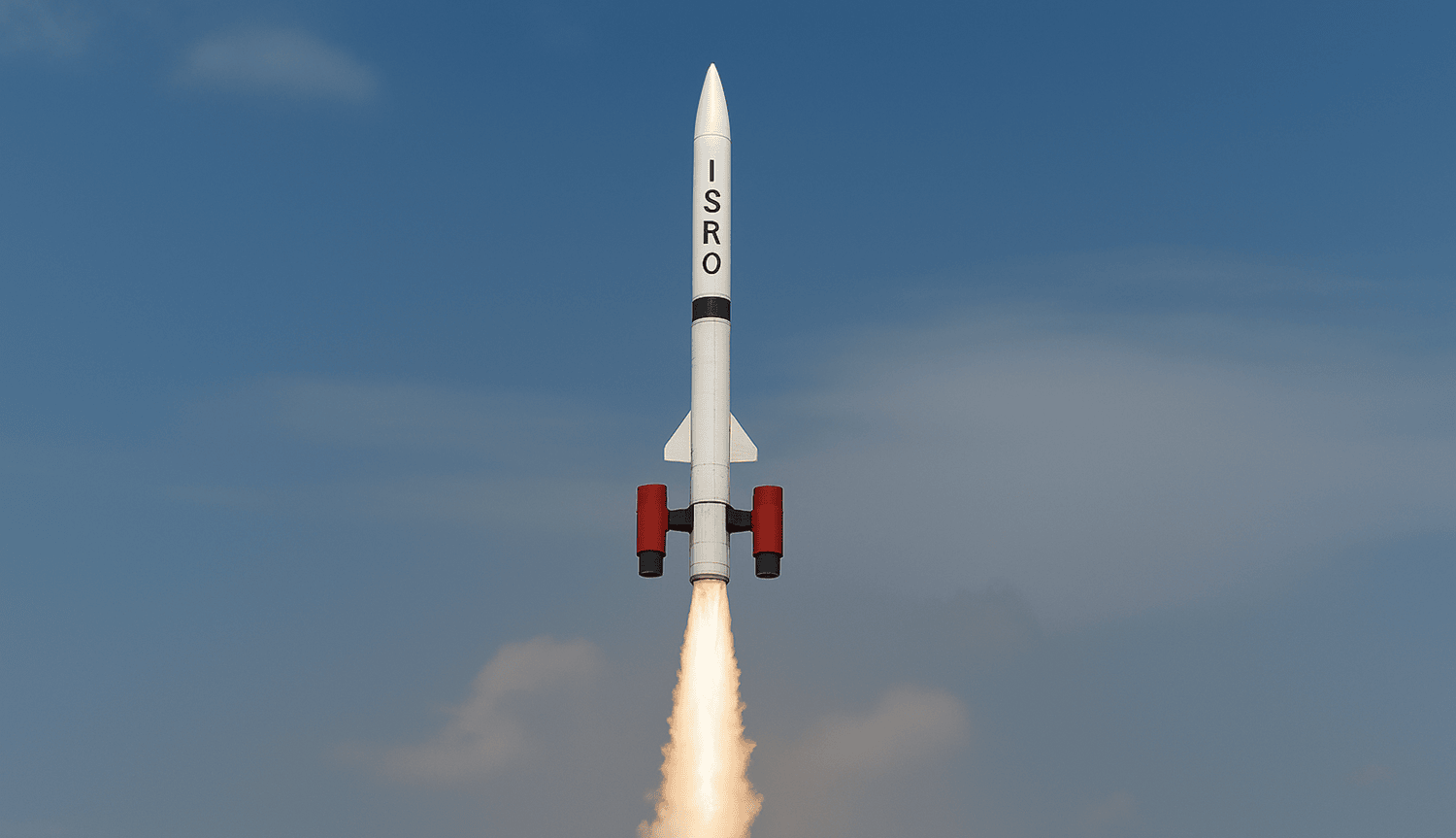
The Indian Space Research Organisation marked a decisive step toward air-breathing launch systems with the first flight of its Scramjet Engine Technology Demonstrator from Satish Dhawan Space Centre, Sriharikota, at 06:00 IST on 28 August 2016. A twelve-hour countdown ended with a clean lift-off of the Advanced Technology Vehicle-D02, a two-stage RH-560 solid booster adapted to carry twin hydrogen-fuelled scramjet modules on the back of its second stage.
Flight telemetry showed each critical event arriving on time: booster burn-out at 39.5 seconds, stage-two ignition at 40 seconds, scramjet light-up at 55 seconds, sustained combustion for five seconds, second-stage tail-off at 65 seconds, and splash-down 300 seconds after launch about 320 kilometres down-range in the Bay of Bengal. Tracking radars at Sriharikota locked the vehicle from lift-off to impact, recording stable flight at Mach 6 in the scramjet window.
Scramjet Engine Demonstrator Validates Air-Breathing Launch Feasibility
Mission highlights:
- Peak dynamic pressure: 80 kPa at 25 km altitude
- Total propellant load: 3.3 tonnes solid, 0.9 kg gaseous hydrogen
- Flight Mach number during scramjet operation: 5.9 ± 0.1
- Combustor pressure rise: 1.7 bar over free-stream
- Specific thrust: 240 N s/kg of airflow
Why this matters:
A scramjet burns fuel in an air stream that stays supersonic through the engine. The design removes heavy liquid-oxygen tanks, trims launch mass, and raises the payload margin. The August test proved four cornerstones:
- Supersonic air intake discipline. The rectangular, flush-mounted inlet captured smooth flow without unstart.
- Reliable ignition at near-instant lighting using a spark torch and pilot hydrogen jet.
- Flameholding stability maintained by staged fuel injection through transverse slots.
- Thermal endurance of nickel-based alloys and ceramic coatings for hundreds of milliseconds in a 1 800 °C core.
ISRO engineers had rehearsed those features on the ground in a free-jet rig at the Vikram Sarabhai Space Centre. The 2016 flight moved proof from the wind tunnel to the sky in a single sweep.
From Ground Rigs to Flight – India’s Hypersonic Scramjet Evolution
Work on air-breathing propulsion in India reaches back to 1993, when ISRO opened a small hypersonic group to study ramjets for a possible Reusable Launch Vehicle (RLV). Bench tests in 2005 produced seven seconds of stable Mach 6 combustion. By 2010 a dedicated Scramjet Engine Integrated System (SEIS) team was in place with computational, materials, and instrumentation specialists.
- Mixed-compression inlet design that balances capture ratio with shock-on-lip tolerance.
- Transitory heating on the cowl lip at Mach 6 airflow, exceeding 60 W/cm².
- Gaseous-hydrogen plumbing rated for cryogenic fill yet weight-safe for sounding rocket use.
- Digital control logic that senses combustor pressure spikes within two milliseconds and trims fuel to keep the flame steady.
The team also wrote a full-scale computational fluid dynamics suite named HyDROP to predict heat flux and pressure waves. Results from HyDROP matched within eight percent of flight data, raising confidence for longer burns later. Similar initiatives, such as Purdue University’s new hypersonics applied research facility, are helping advance experimental capabilities worldwide.
Design Philosophy Behind India’s Scramjet Flight Vehicle
The Advanced Technology Vehicle (ATV-D02) used on 28 August carried no payload other than sensors. Its purpose lay in reaching the right speed-altitude box and holding attitude long enough to judge engine output. The ATV stack stood 12.8 meters tall, spun at 2.5 radians per second for passive stability, and relied on cold-gas thrusters for pitch trim after stage separation. The scramjet nacelles sat flush beneath a titanium shroud to reduce drag until ignition.
Designers kept moving parts to a minimum. The only actuators were the hydrogen valves that opened one-tenth of a second before spark. Once lit, the flame drew in atmospheric oxygen, cutting oxidiser mass to zero and saving roughly 200 kilograms versus a comparable rocket second stage.
Global Benchmarks in Hypersonic Scramjet Testing
With this flight India joined the United States, Russia, and China in demonstrating in-air scramjet combustion. Each programme, however, takes a distinct route. NASA’s X-43A reached Mach 9.7 in 2004 on a drop-and-dash profile. Russia’s GLL-AP used a wing-body to test at Mach 6 over the Baikonur range. China’s JF-12 tunnel fed data for its Starry Sky-2 boost-glide craft. ISRO chose the low-cost sounding rocket path, accepting shorter burn time in exchange for quick-turn learning cycles.
Next steps announced in 2016
At the post-flight briefing ISRO Chairman A. S. Kiran Kumar laid out a staged plan:
- A second flight to extend scramjet firing to 20 seconds.
- The wind tunnel runs at Mach 7 to refine inlet shock control.
- Coupling of an air-breathing cruise stage to a reusable first stage within a decade.
He stressed cost rather than speed: a tenfold cut in launch price could follow the full adoption of air-breathing first stages blended with conventional upper stages.
Besides space launches, a scramjet culture boosts India’s defense labs. Shared test data flow to the Defence Research and Development Organisation (DRDO) for future tactical systems. Materials forged for 1 800 °C incident heat will serve turbine blades and high-temperature fuel tanks. Universities gain too. The Indian Institute of Science, IIT-Kanpur, and IIT-Madras all logged sensor packages aboard ATV-D02, giving students live hypersonic data for thesis work.
Engineers had left Sriharikota with a firm measurement: five seconds of clean thrust at Mach 6. For a program run on a shoestring, the flight proved both frugal design and bold ambition. The next trial, they said, would answer two questions still open: Can the flame stay locked when the vehicle noses above 30 kilometers? And will the inlet keep swallowing air when boundary-layer thickness grows? Answers to both would steer the schedule for India’s future RLV stage.
ISRO Future Missions and Hypersonic Systems – March 2025 Update
Nine years on, the air-breathing roadmap drawn in 2016 no longer looks cautious. It looks prophetic.
ISRO matched its promise with action in September 2020 when DRDO’s Hypersonic Technology Demonstrator Vehicle rode a solid booster from Wheeler Island and kept its scramjet alive for twenty seconds at roughly Mach 6.2. That run confirmed hydrogen mixing lessons from 2016 and transferred control logic unobtrusively revised for longer burns.
Hypersonic Technology Vehicle and RLV Landings Tighten System Integration
The next leap arrived on 22 July 2024. Engineers fitted two improved scramjets to a Rohini RH-560 and fired them for 22 seconds over the Bay of Bengal. Instrument tapes later showed a flawless pressure curve with less than two percent thrust decay across the window. This milestone drew comparisons with the U.S. Army’s hypersonic engine test programs planned for 2026. The event, low-key in the evening news, mattered more than a television countdown. It proved ignition margins at higher altitudes where static pressure drops below 8 kPa. The inlet held shocks in place; the combustor stayed rich enough to burn, not so rich that it quenched. That balance was the needle ISRO tried to thread for eight years.
Scramjet maturity then meshed with reusable-flight progress. On 23 June 2024, the Reusable Launch Vehicle (RLV) Landing EXperiment scored its third straight autonomous touchdown at Chitradurga. The unpowered approach carried a revised belly shield lined with the same SiC-Si₃N₄ tiles qualified in the scramjet rig. The crossover trimmed program risk: a tile that protects an RLV also guards an inlet lip.
Ground Test Breakthroughs in Long-Duration Hypersonic Combustion
January 2025 pushed the technology fence again. DRDO’s Defence Research and Development Laboratory reported a 120-second scramjet combustor ground run at Mach 6 free-stream, the longest such test in India. The rig in Hyderabad maintained chamber pressure inside a shock tunnel for two full minutes with no flameout. Engineers credited a new coaxial-jet flameholder first sketched on ISRO drawing boards in 2018. A week later a shorter, brutal endurance run at 2 700 °C simulated the thermal spike of ascent—confidence rose that the engine shell would not warp under flight heat flux.
Momentum gathered. In February, the Hypersonic Steering Committee, a joint ISRO-DRDO body, cleared funds for a flight known as ATV-D03. The booster will use two S-12K strap-ons to reach Mach 6.5, shut them and then relight the scramjet for forty seconds. Lift-off now targets the third quarter of 2025, subject to range bookings.
Shift to Dual-Fuel Scramjet Strategy Reduces Ground Handling Costs
Beyond raw burn time, fuel choice has shifted. Teams once bound to pure hydrogen now eye a hydrocarbon start, switching to hydrogen mid-run. The dual-fuel scheme halves ground-handling cost. Preliminary mixing tests in early March showed a 15-percent drop in ignition delay when methane led the sequence.
Hardware alone does not tell the whole story. Data culture changed too. All scramjet flights since 2024 stream pressure plots into a cloud archive at the National Super-Computing Mission node in Bengaluru. This lets university partners run models inside hours instead of waiting months for tape copies. That open door spurred two dozen doctoral projects from supersonic combustion noise to regeneratively cooled liners.
Expanding Industrial Impact and Strategic Defense Potential
Hindustan Aeronautics now machines the dual-wall combustor shells from a cobalt alloy stack built for scramjet duty and for the HAL-29 afterburner. A production cell finished its first overseas order to a European research consortium in February. Air-breathing propulsion is no longer a curiosity. It is shaping a small but growing industrial lane.
Security watchers notice, of course. With the 2020 HSTDV proving guidance logic and the 2025 ground runs proving long-life combustion, India can at least contemplate a scramjet-based tactical missile. Officials stay guarded, yet informal briefings hint at a 1 500-kilometre class weapon arriving late decade. Whether that system ever flies as a defense article, the work already sharpens launch-vehicle design.One last change sits in plain sight. Launch cost curves that once relied on mass production alone now fold in free oxygen. ISRO projects a reusable, air-breathing first stage that could cut per-kilogram cost to low Earth orbit to under USD 900. Analysts note that such air-breathing systems share challenges with other advanced propulsion concepts, including thermal management, fuel handling, and scalability for operational missions. That estimate rides on a scramjet phase lasting 100 seconds, debris-free recovery of the stage at down-range bases, and re-entry shields drawn directly from RLV test flights. The path is steep, yet each bench and flight result pushes the slope flatter.
REFERENCE SOURCES
- https://thedefensepost.com/2025/04/28/india-hypersonic-engine-test/
- https://www.isro.gov.in/ScramjetEngine.html
- https://www.asianscientist.com/2016/08/tech/india-scramjet-engine-test-isro-aug-2016/
- https://www.satellitetoday.com/government-military/2016/08/29/isro-launches-scramjet-engine-demonstration-mission/
- https://www.pib.gov.in/Pressreleaseshare.aspx?PRID=1651956
- https://indianexpress.com/article/explained/explained-sci-tech/drdo-scramjet-test-hypersonic-weapons-9795405/
- https://www.isro.gov.in/ISROflightexperimentAirBreathingPropulsionSystem.html
- https://www.eurasiantimes.com/isros-hypersonic-test-could-make-it-1st-space-agency-to-place-a-satellite-using-scramjet-powered-reusable-launch-stage/
- https://www.indiasentinels.com/defence-industry/drdo/drdo-advances-hypersonic-missile-programme-with-successful-1000-second-scramjet-test-6773
- https://www.isro.gov.in/ISRO_Completes_RLV_Technology_Demonstrations_RLV-LEX3.html